Sabot Profiler (REBAR)
The Sabot Profiler is a one-dimensional structural analysis of the projectile/sabot system caused by longitudinal accelerations within the barrel. The software calculates the nominal axial stress distribution along the length of the projectile and can be used to optimize the shape (mass) of the selected piece parts, primarily sabots for long rod applications. The predicted stress levels obtained are very close to those obtained by more detailed Finite Element Method (FEM) solutions. Therefore, Profiler can be used as an efficient optimization tool.
The output parameters calculated for the projectile/sabot system caused by the longitudinal accelerations within the barrel are then used to perform the In Bore Balloting analysis.
- Assess Stress and shear levels within the sabot
- Assess compression tension loads on projectile penetrator buttress grooves
- 1D Structural Analysis for maximizing muzzle velocity via Sabot Design
- Analyzes set back Load and stress and strain levels of
- Penetrator core at grooves
- First and Last Buttress groove location
- Groove Minimum Diameter
- Material Properties
- Penetrator core at grooves
- Sabot
- Material properties
- Analyzes set back Load and stress and strain levels of
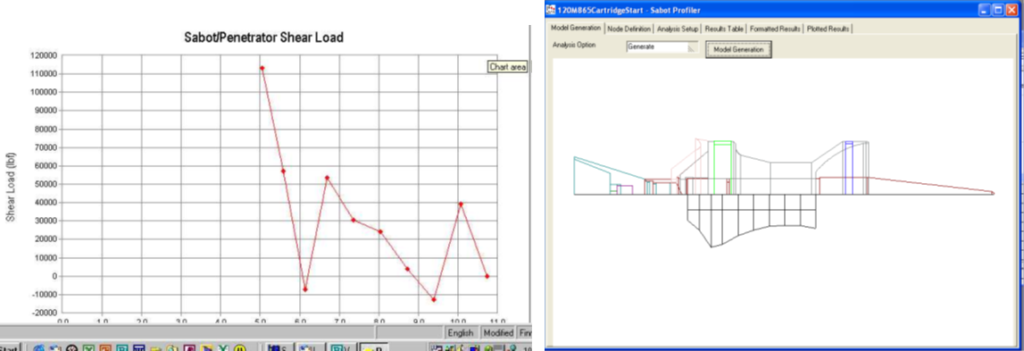
Cartridge Case Analysis System
Simulate Case Deflections & Chamber Interaction during firing pressurization
The modeling and analysis of a cartridge case requires an elastic-plastic, thermal, and dynamic solution. The use of general-purpose finite element programs for case analysis can be very expensive and labor-intensive because the model must contain many elements to obtain stress distributions in the thin cylindrical wall region of the case and in the base region. Additionally, the case material can exceed its yield point for a large part of the interior ballistic cycle, requiring an inelastic analysis with relatively long computation times.
To improve computational and parametric design efficiency, Arrow Tech Associates, Inc. has developed an analytical tool specifically to analyze cartridge cases, called CASAS (CASe Analysis System).
CASAS is a primary analytical tool to perform the elastic-plastic, dynamic analysis (including transient heat effects) required for cartridge case design.
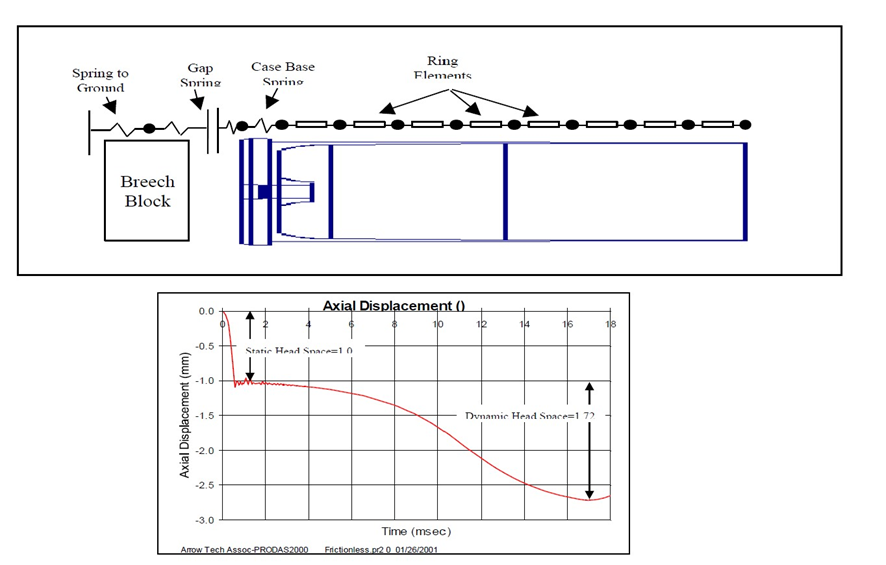
- CASAS simulates the dynamic interaction of the cartridge case and gun chamber in five (5) phases of the firing cycle:
- Initial Conditions (definition of material properties such as modulus, density, coefficient of thermal expansion, thermal conductivity, along with case-chamber gaps & bolt stiffness.)
- Propellant Ignition (initial case contact with the chamber wall.)
- Pressure Load Increase to Maximum (maximum composite structure deflection)
- Elastic case recovery as the internal pressure decays to atmospheric conditions.
- Residual Case/Chamber condition clearance or interference between the case and the chamber, case extraction force.
- CASAS is ideal for performing the following case/chamber parametric studies:
- Dimensional
- Stress-Strain Curve
- Chamber Pressure
- Friction Coefficient
- Extraction Temperature
- Case/Chamber Gap Size
- Static Head Space
- Dynamic Head Space
- CASAS output includes:
- Maximum Total Plastic Case Strain (assess case failure)
- Extraction force required
- Maximum Bolt Load
In Bore Balloting (BALANS)
Complete simulation of projectile/gun interaction during interior ballistics cycle and then flyout to target
Simulates the Dynamic Response and Interaction of a Flexible Projectile and a Flexible Gun Tube During In-Bore Travel
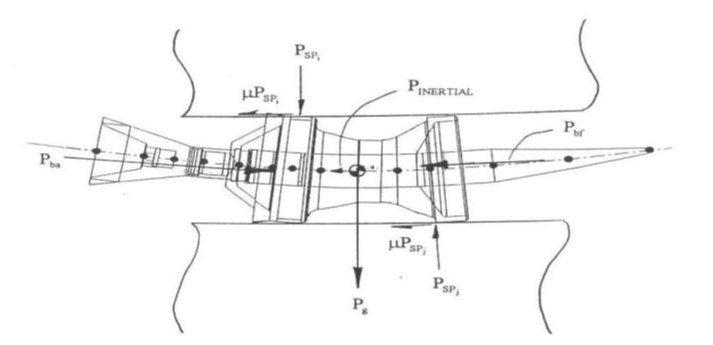
Using BALANS you can describe the projectile and tube with up to 50 lumped mass nodes and connecting beams each, compute the deflection of the projectile and gun tube during movement of the projectile from breech to muzzle exit, and, determine the balloting contribution to disper-sion.
BALANS analyzes the dynamic response and interaction of a statistically representative, flexible projectile and a flexible gun tube during in-bore travel., in a time-step iterative solution. BALANS assumes the projectile is initially misaligned in the gun tube due to manufacturing tolerances. During firing, this misalignment produces secondary forces causing transverse displacement and yawing motion of the projectile as it travels from breech to muzzle.
The resulting yaw angle and the angular rate at muzzle exit are then analyzed for their effect on dispersion.
BALANS features the following:
- Projectile Modeling
- Gun Tube Modeling
- Bore profile definition
- Forcing Function Definition
- Initial Condition Definition
- Automated Statistical Evaluation of Dispersion
- Gun Tube
- Motion
- Muzzle Exit Transverse Velocity
- Projectile
- Motion
- Shape
- Stress
- Projectile / Tube Interface Reaction Loads
- Tube Support Reaction Loads
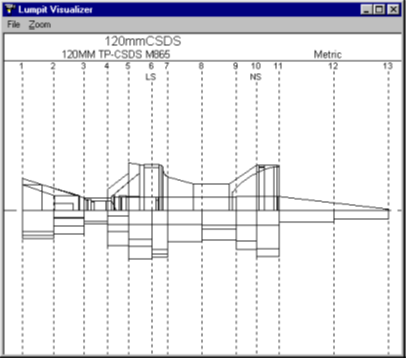
- Monte Carlo error Sources
- Run Internal Balloting on 500 cases
- Collect Angular Rates at Muzzle
- Run Body Fixed Six Dof for each set of angular rates to target impact
- Calculate dispersion performance on target